Introduction
The following is our group introduction to ultrasonic machining technology. Ultrasonic machining is a process in which a vibration at an ultrasonic amplitude is utilized as the cutting tool. The abrasive slurry is driven between the tool and the workpiece, resulting in abrasive impacts polishing the machined parts. In fact, the locally existing material is removed in the form of powder, which is done to provide holes and slots; the workpieces can also be bonded together with the assistance of ultrasonic vibrations. Ultrasonic technology is one of the specialized machining techniques and is applied to many materials difficult to machine by conventional methods.
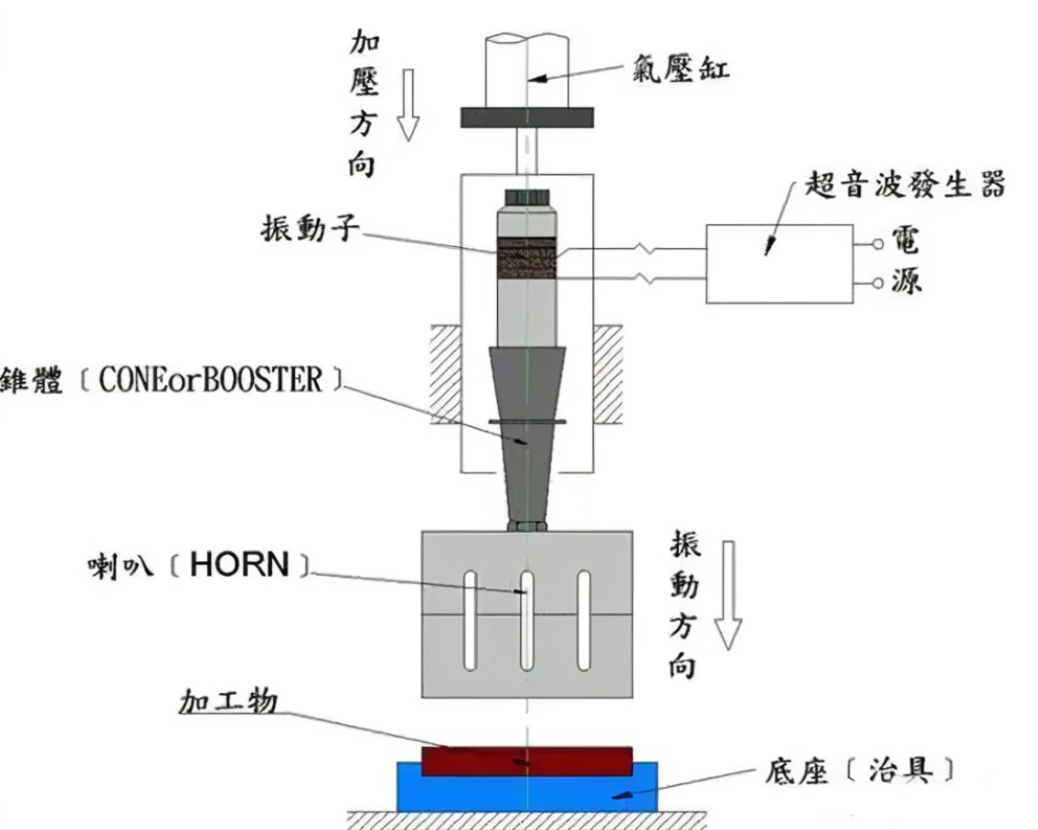
I. Types of Ultrasonic Machining Applied
- Ultrasonic removal machining
- Ultrasonic surface finishing
- Ultrasonic welding
- Ultrasonic treatment
II. Ultrasound and Its Characteristics
1. Types of Sound Waves
- Audible sound waves: Sound waves whose frequencies range between 16 Hz and 16000 Hz.
- Infrasound waves: Sound waves of frequencies below 16Hz.
- Ultrasonic waves: Sound waves of frequencies above 16000 Hz.
- Hypersound waves: Sound waves having a frequency higher than 1010 Hz.
2. Fundamental Properties of Ultrasonic Waves
- Ultrasonic waves, just like sound waves, can have a transmission through several elastic media like gases, liquids, and solids at different velocities.
- Ultrasonic waves can carry great amounts of energy to act upon all the obstacles that can forward in the route of propagation to cause sound pressure. Since being a type of longitudinal wave, the Energy intensity of ultrasonic waves can be measured with the help of energy density, which is as great as more than about 100W/cm².
- Ultrasonic waves produce strong shockwaves and cavitation effects in liquid media; this acts to intensify the machining work.
- The incidence of ultrasonic waves causes reflection, interference, and resonance phenomena by wave superpositions. This intensifies machining energy.
III. Principles and Characteristics of Ultrasonic Machining
1. Basic Principles of Ultrasonic Machining
Ultrasonic machining is a machinability process that employs ultrasonic power in driving abrasive grains at a very high speed to impact the surface of a workpiece, leading to the destruction or cutting of the material. The process is as follows:
- An ultrasonic generator to transfer AC power into ultrasonic electric oscillation
- A transducer to transfer the electric oscillation into mechanical vibration
- An amplitude transformer amplifies the vibration of 0.05 ~ 0.1mm, which is powerful enough to drive the tool to vibrate ultrasonically.
- The tool propels the abrasives to impact and polish the workpiece, making the surface material break and remove
- Hydraulic shock waves and cavitation produced by the working fluid accelerate the cracking and destruction of the surface material.
- A mix of mechanical impact, polishing, and cavitation effects in ultrasonic machining, with impact being the primary action.
2. Characteristics of Ultrasonic Machining
- Capable of machining all types of hard and brittle materials, especially non-conductive nonmetallic materials like glass, ceramics, quartz, gemstones, and diamonds.
- Tools may be fabricated from softer materials to cut unique shapes.
- Simple relative motion between the tool and the workpiece—thus simple machine structure.
- Low cutting force and heat, thus preventing deformation and burns, with high machining precision and surface quality.
IV. Ultrasonic Machining Equipment
- The basic constituent components of ultrasonic machining equipment are also termed ultrasonic machining devices, and these are :
- Ultrasonic Generator: This constituent component changes the mains AC power to ultrasonic frequency electrical oscillation.
- Acoustic Components: A transducer, an amplitude transformer, and a tool that translates high-frequency electrical energy into mechanical vibration and this amplifies the same for the high-frequency, small-amplitude vibration of the tool during ultrasonic machining.
V. Applications of Ultrasonic Machining Technology
- Machining Applications
- While having a relatively lower production rate than EDM and ECM, it has better machining precision and surface quality.
- It is used for machining hard and brittle materials like semiconductors, and non-metal materials like glass, ceramics, quartz, silicon, agate, gemstones, and diamonds.
- Polishing/fine finishing of hard molds and dies after EDM to decrease the surface roughness.
- Types of Machining
- Hole Machining: The workpiece materials that are chiefly machined by ultrasonic machining process are only round holes, shaped holes, cavities, slots, and micro-holes in brittle hard materials.
- Cutting Machining: Ultrasonic machining provides thin slicing, narrow cuts, high precision, high productivity, and good economy in cutting brittle hard materials like ceramics, quartz, silicon, and gemstones.
- Ultrasonic Cleaning: It develops cavitation effects in cleaning liquid to wash out dirt from complex geometric shapes and high-precision small parts, especially for deep small holes, micro-holes, blind holes, grooves, and narrow slits. Used for cleaning semiconductors, integrated circuits, instruments, electrical vacuum devices, optical parts, and medical devices.
- Ultrasonic Welding
- This process involves removing oxide films on the surfaces of workpieces by means of ultrasonic vibration, thus making them stick through high-speed vibrational impacts and frictional heat.
- Used in welding nylon, plastics, and aluminum products prone to oxide formation, and improving weldability of ceramics and other non-metals which are coated with tin or silver. Also welds rare metals such as titanium and molybdenum.
- Composite Machining
- The modification of ultrasonic machining by combining it with ECM or EDM enhances the speed and minimizes tool wear while machining hard metals such as carbide and heat-resistant alloys.
- Non-Destructive Testing
- Uses ultrasonic waves for nondestructive testing in distance measurement, control, monitoring, and material measurement with its ability to reflect, transmit, and penetrate most materials.
- Everyday Applications of Ultrasonic Technology
- Cleaning dust, promoting plant growth, underwater reconnaissance, medical diagnostics, etc.
Conclusion:
Hence, all hopes are high and the horizon seems endless for the future of ultrasonic machining technology.
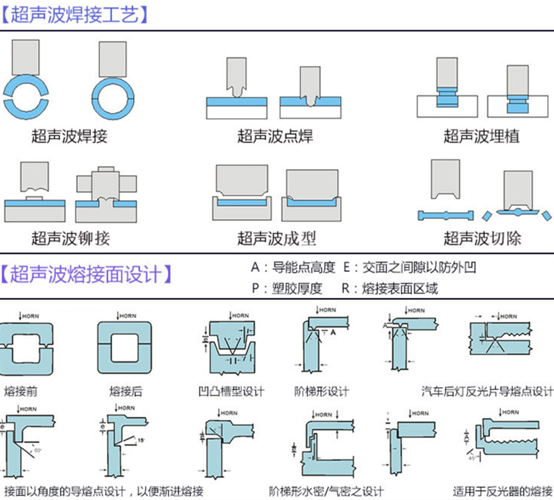
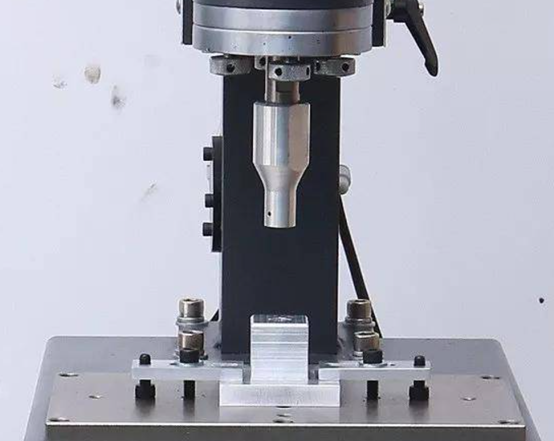