(I) Concept of Sandblasting
Sandblasting is a process meant to clean, process, or prepare an object's surface using speedy abrasive particles. It is applied industrially quite well in manufacturing, construction, and maintenance for the removal of surface dirt, rust, old coatings, or oxidation layers to expose a clean surface, increasing the surface area for paint, adhesives, or coatings to adhere to.
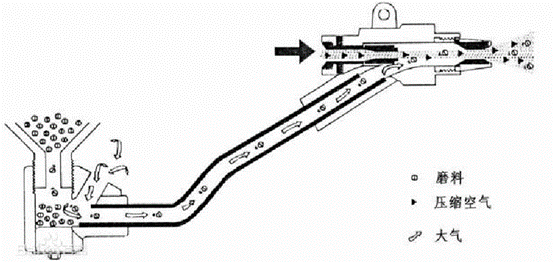
(II) Application Range
- Metal Processing: Sandblasting in metal manufacturing and processing makes way for the elimination of the layers of oxidation, rust, oil stains, and other dirt to prepare the surface for subsequent processing, either by welding or painting.
- Shipbuilding and Offshore Engineering: In the shipbuilding and off-shore engineering, sandblasting finds an application in the maintenance and repair of ships by removing old paint layers and marine biofouling on the hull for re-coating and protection.
- Construction: It can be used to clean concrete and, hence, prepare concrete surfaces for new coatings or adhesives in the building and construction industry.
- Automobiles and Motorcycles: Sandblasting is applied at automobile and motorcycle manufacturing lines and in service stations to clean old paint layers, rust, and welding burns.
- Aerospace: Aerospace industries use sandblasting to clean aircraft parts and components for exacting coating adhesion and material performance.
- Plastics/Glass: Sandblasting is used to increase the surface roughness of plastic and glass products to increase the effect of printing, coating, or adhesion.
- Stone and Tiles: In the processing of stones and tiles, sandblasting is used to clean the surface dirt and loose materials and provide certain textures and finishes.
- Art and Decoration: This is also used to create artistic purposes and decoration, as this method of creating such patterns and texts on glass or metal.
- Archaeology: Sandblasting might find an application in archaeological digs for the gentle cleaning of objects unearthed to reveal hidden details and features.
- Restitution and Preservation: This entails restorative sandblasting of historic buildings or antiquated objects whereby the elimination of dirt and other old coatings leaves very little preening on the original surface.
Pre-treatment Stage
The pre-treatment in sandblasting involves the treatment of the workpiece surface before coating or electroplating.
The quality of the pre-treatment would determine the adhesion, appearance, moisture resistance, and corrosion resistance of the coating.
Poor pretreatment may leave the continuation of corrosion under the coating and can peel off in sheets. If the surface is properly cleaned and a simply cleaned workpiece has the same coating applied, the life span can be different by 4-5 times.
Some common methods of cleaning include Solvent Cleaning, Pickling, Manual Tools, and Power tools. Process Stage Sandblasting is a process using compressed air as the power to form a high-velocity jet stream that causes changes on the surface of a workpiece by impinging abrasive material onto the workpiece surface. The action of impingement and cutting of abrasive on the workpiece surface will provide some degree of cleanliness and roughness, which enhances mechanical performance on the workpiece surface.
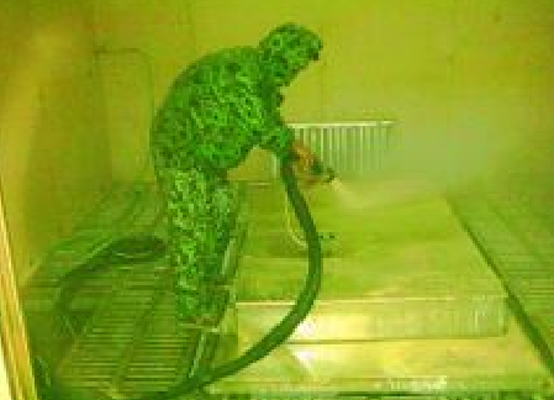
(III) Relevant Machinery
The most popular products used for abrasive jet applications are the sandblasting machines. It is normally divided into dry sandblasting machines and liquid sandblasting machines. Dry sandblasting machines are further classified as the suction type and pressure type.
Suction Type Dry Sandblasting Machine
- General Composition
- Working Principle
Pressure Type Dry Sandblasting Machine
- General Composition
- Working Principle
Liquid Sandblasting Machine
Compared with dry sandblasting machines, one of the most advantageous characteristics of liquid sandblasting machines is to control dust pollution during the sandblasting process and offer a better working environment.
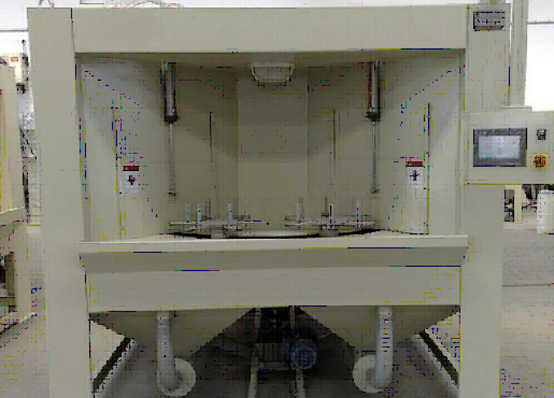
- General Composition
- Working Principle
The well-mixed slurry, which is a mixture of abrasive and water, is sent into the spray gun by a slurry pump.
Compressed air serves as the accelerating power to the slurry and is fed into the spray gun via an air supply pipe. In this gun, the compressed air accelerates the slurry and then sprays out from the nozzle onto the processed surface for the desired processing purpose. In liquid sandblasting machines, the slurry pump acts as the supply power and compressed air as the acceleration power.
(IV) Other Grades of Cleanliness
There are two internationally representative standards of cleanliness. One is the "SSPC-" standard formulated by the United States in 1985, and another is the "Sa-" standard formulated by Sweden in 1976. The latter is further divided into four grades: Sa1, Sa2, Sa2.5, and Sa3. These are normally used internationally and have the following detailed contents:
- Sa1 Level: This is equivalent to SSPCSP7 of America. The cleaning procedure involves simple manual brushing and sanding methods. It is the lowest intensity of the four cleanliness levels. It gives little more protection than those workpieces which are not treated.
- Technical standard of the treatment at Sa1 level: Workpiece surface shall not be visibly oily or greasy or shall not have residual oxide scales, rust spots, and residual paint.
- Sa2 Level: his is equivalent to SSPC-SP6 in the US. This level uses the sandblasting cleaning method, being at the lowest grade within the category of sandblasting. It will suffice for general requirements but offers protection much better than manual brushing.
- Technical standard for Sa2 level treatment: No grease or oil layer shall exist, and the workpiece surface shall neither obviously have dirt and contaminants nor be oxidized, rusty, painted, and oxidized; also, no corrosion and other foreign substances are allowed, except for defects, which shall not exceed an area of 0.33 square meters per square meter of the surface area.
- Sa2.5 Grade: This is the most commonly used grade in the industry and is generally considered to be an acceptance technical requirement and, in fact, a standard. The cleaning level at near white.
- The technical standard of treatment at the Sa2.5 level: is the same as for Sa2; however, the defects should not be more than 5% of the surface area per square meter.
- Sa3 Level: This is the topmost grade in the industry, which is regarded as the SSPC-SP5 of the USA. It is also known by the alternative name of white cleaning level.
- Technical standard for Sa3 level treatment: no shadows, defects, rust, etc., but otherwise same as Sa2.5. Sandblasting Materials
Sandblasting Materials
Sandblasting: A term used in gold and silver coin minting technology. It refers to the process of using metal sand particles of various sizes to create a very fine matte surface on the pattern part of the production molds. When producing gold and silver coins, this results in a beautiful silver layer on the pattern part, enhancing the three-dimensional and layered effect.
Sandblasting (refers to rust removal or coating on metal surfaces) uses quartz sand, ordinary quartz sand, and refined quartz sand: characterized by high hardness and good rust removal effect. The physical and chemical specifications are as follows:
- SiO2: 88—99.8%
- Fe2O3: 0.1—0.005%
- Refractoriness: 1450---1800°C
- Appearance: Uniform particles, commonly used sizes are 1-3MM and 0.1-0.3MM, pure white. The granularity range is mostly between 5—220 mesh, and can be produced according to user requirements.
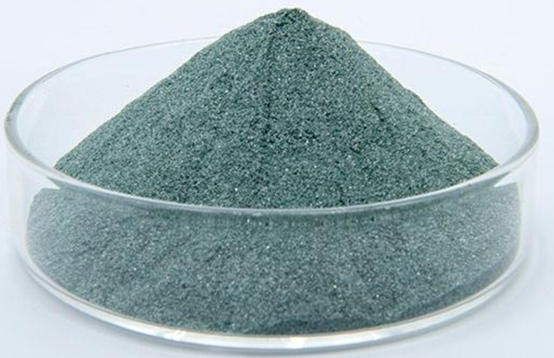
Sandblasting Parts:
Sandblasting Rubber Hoses: both the inner and outer layers of the sandblasting hoses are made of abrasion resistance materials, mainly NBR and SBR, or some imported ones with better performance adopted PARA rubber; the common abrasion resistance coefficient is 60-75 cubic millimeters.
(V) Operation MethodsProduct Structural Design Secondary Processing Specification – Sandblasting
(I) Concept of Sandblasting
Sandblasting is a process meant to clean, process, or prepare an object's surface using speedy abrasive particles. It is applied industrially quite well in manufacturing, construction, and maintenance for the removal of surface dirt, rust, old coatings, or oxidation layers to expose a clean surface, increasing the surface area for paint, adhesives, or coatings to adhere to.
(II) Application Range
- Metal Processing: Sandblasting in metal manufacturing and processing makes way for the elimination of the layers of oxidation, rust, oil stains, and other dirt to prepare the surface for subsequent processing, either by welding or painting.
- Shipbuilding and Offshore Engineering: In the shipbuilding and off-shore engineering, sandblasting finds an application in the maintenance and repair of ships by removing old paint layers and marine biofouling on the hull for re-coating and protection.
- Construction: It can be used to clean concrete and, hence, prepare concrete surfaces for new coatings or adhesives in the building and construction industry.
- Automobiles and Motorcycles: Sandblasting is applied at automobile and motorcycle manufacturing lines and in service stations to clean old paint layers, rust, and welding burns.
- Aerospace: Aerospace industries use sandblasting to clean aircraft parts and components for exacting coating adhesion and material performance.
- Plastics/Glass: Sandblasting is used to increase the surface roughness of plastic and glass products to increase the effect of printing, coating, or adhesion.
- Stone and Tiles: In the processing of stones and tiles, sandblasting is used to clean the surface dirt and loose materials and provide certain textures and finishes.
- Art and Decoration: This is also used to create artistic purposes and decoration, as this method of creating such patterns and texts on glass or metal.
- Archaeology: Sandblasting might find an application in archaeological digs for the gentle cleaning of objects unearthed to reveal hidden details and features.
- Restitution and Preservation: This entails restorative sandblasting of historic buildings or antiquated objects whereby the elimination of dirt and other old coatings leaves very little preening on the original surface.
Pre-treatment Stage
The pre-treatment in sandblasting involves the treatment of the workpiece surface before coating or electroplating.
The quality of the pre-treatment would determine the adhesion, appearance, moisture resistance, and corrosion resistance of the coating.
Poor pretreatment may leave the continuation of corrosion under the coating and can peel off in sheets. If the surface is properly cleaned and a simply cleaned workpiece has the same coating applied, the life span can be different by 4-5 times.
Some common methods of cleaning include Solvent Cleaning, Pickling, Manual Tools, and Power tools. Process Stage Sandblasting is a process using compressed air as the power to form a high-velocity jet stream that causes changes on the surface of a workpiece by impinging abrasive material onto the workpiece surface. The action of impingement and cutting of abrasive on the workpiece surface will provide some degree of cleanliness and roughness, which enhances mechanical performance on the workpiece surface.
(III) Relevant Machinery
The most popular products used for abrasive jet applications are the sandblasting machines. It is normally divided into dry sandblasting machines and liquid sandblasting machines. Dry sandblasting machines are further classified as the suction type and pressure type.
Suction Type Dry Sandblasting Machine
- General Composition
- Working Principle
Pressure Type Dry Sandblasting Machine
- General Composition
- Working Principle
Liquid Sandblasting Machine
Compared with dry sandblasting machines, one of the most advantageous characteristics of liquid sandblasting machines is to control dust pollution during the sandblasting process and offer a better working environment.
- General Composition
- Working Principle
The well-mixed slurry, which is a mixture of abrasive and water, is sent into the spray gun by a slurry pump.
Compressed air serves as the accelerating power to the slurry and is fed into the spray gun via an air supply pipe. In this gun, the compressed air accelerates the slurry and then sprays out from the nozzle onto the processed surface for the desired processing purpose. In liquid sandblasting machines, the slurry pump acts as the supply power and compressed air as the acceleration power.
(IV) Other Grades of Cleanliness
There are two internationally representative standards of cleanliness. One is the "SSPC-" standard formulated by the United States in 1985, and another is the "Sa-" standard formulated by Sweden in 1976. The latter is further divided into four grades: Sa1, Sa2, Sa2.5, and Sa3. These are normally used internationally and have the following detailed contents:
- Sa1 Level: This is equivalent to SSPCSP7 of America. The cleaning procedure involves simple manual brushing and sanding methods. It is the lowest intensity of the four cleanliness levels. It gives little more protection than those workpieces which are not treated.
- Technical standard of the treatment at Sa1 level: Workpiece surface shall not be visibly oily or greasy or shall not have residual oxide scales, rust spots, and residual paint.
- Sa2 Level: his is equivalent to SSPC-SP6 in the US. This level uses the sandblasting cleaning method, being at the lowest grade within the category of sandblasting. It will suffice for general requirements but offers protection much better than manual brushing.
- Technical standard for Sa2 level treatment: No grease or oil layer shall exist, and the workpiece surface shall neither obviously have dirt and contaminants nor be oxidized, rusty, painted, and oxidized; also, no corrosion and other foreign substances are allowed, except for defects, which shall not exceed an area of 0.33 square meters per square meter of the surface area.
- Sa2.5 Grade: This is the most commonly used grade in the industry and is generally considered to be an acceptance technical requirement and, in fact, a standard. The cleaning level at near white.
- The technical standard of treatment at the Sa2.5 level: is the same as for Sa2; however, the defects should not be more than 5% of the surface area per square meter.
- Sa3 Level: This is the topmost grade in the industry, which is regarded as the SSPC-SP5 of the USA. It is also known by the alternative name of white cleaning level.
- Technical standard for Sa3 level treatment: no shadows, defects, rust, etc., but otherwise same as Sa2.5. Sandblasting Materials
Sandblasting Materials
Sandblasting: A term used in gold and silver coin minting technology. It refers to the process of using metal sand particles of various sizes to create a very fine matte surface on the pattern part of the production molds. When producing gold and silver coins, this results in a beautiful silver layer on the pattern part, enhancing the three-dimensional and layered effect.
Sandblasting (refers to rust removal or coating on metal surfaces) uses quartz sand, ordinary quartz sand, and refined quartz sand: characterized by high hardness and good rust removal effect. The physical and chemical specifications are as follows:
- SiO2: 88—99.8%
- Fe2O3: 0.1—0.005%
- Refractoriness: 1450---1800°C
- Appearance: Uniform particles, commonly used sizes are 1-3MM and 0.1-0.3MM, pure white. The granularity range is mostly between 5—220 mesh, and can be produced according to user requirements.
Sandblasting Parts:
Sandblasting Rubber Hoses: both the inner and outer layers of the sandblasting hoses are made of abrasion resistance materials, mainly NBR and SBR, or some imported ones with better performance adopted PARA rubber; the common abrasion resistance coefficient is 60-75 cubic millimeters.
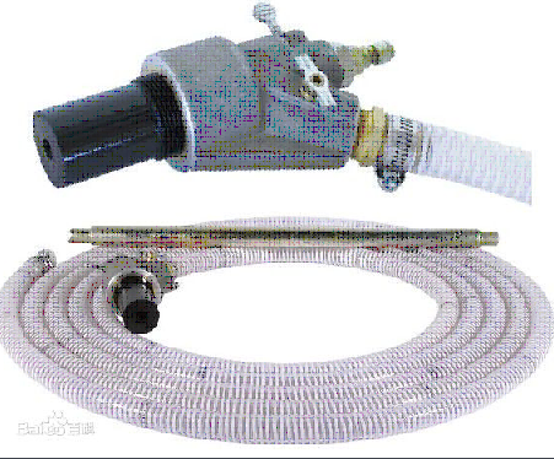
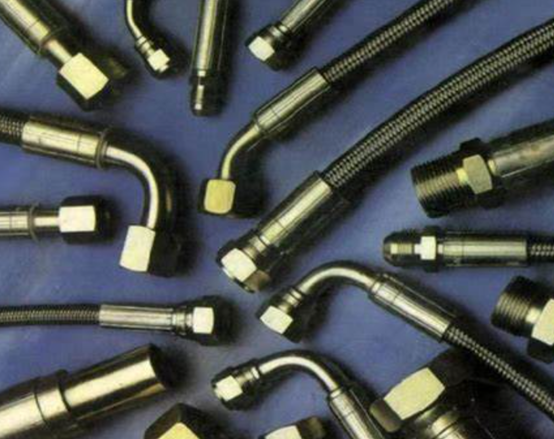
(V) Operation Methods
- Preparation: the work area shall be safe; if necessary, individual protective equipment such as helmets, goggles, gloves, and protective clothes shall be worn.
- Equipment check: Sand-blasting machine, sand-blasting gun, air compressor, abrasive storage container, and the conveying system—check whether they are in proper working condition.
- Abrasive selection: Apply the right abrasive for both the type of material and the condition of the surface that is to be treated: quartz sand, steel shots, glass beads, and plastic particles.
- Sandblasting Operation: Switch on the sandblaster; convey the abrasive from its container, through a conveying system, to the sand-blasting gun, and shoot at high pressure onto the surface of the object.
- Cleaning and Inspection: Clean up the surface after sandblasting from any residual abrasives and loose materials; inspect whether the surface meets the expected effect of treatment.
Other advantages of sandblasting include improved adherence to the applied coating, smoother and more uniform surface, and eliminating the defects on the surface, which can result in corrosion or damage.
- Preparation: the work area shall be safe; if necessary, individual protective equipment such as helmets, goggles, gloves, and protective clothes shall be worn.
- Equipment check: Sand-blasting machine, sand-blasting gun, air compressor, abrasive storage container, and the conveying system—check whether they are in proper working condition.
- Abrasive selection: Apply the right abrasive for both the type of material and the condition of the surface that is to be treated: quartz sand, steel shots, glass beads, and plastic particles.
- Sandblasting Operation: Switch on the sandblaster; convey the abrasive from its container, through a conveying system, to the sand-blasting gun, and shoot at high pressure onto the surface of the object.
- Cleaning and Inspection: Clean up the surface after sandblasting from any residual abrasives and loose materials; inspect whether the surface meets the expected effect of treatment.
Other advantages of sandblasting include improved adherence to the applied coating, smoother and more uniform surface, and eliminating the defects on the surface, which can result in corrosion or damage.
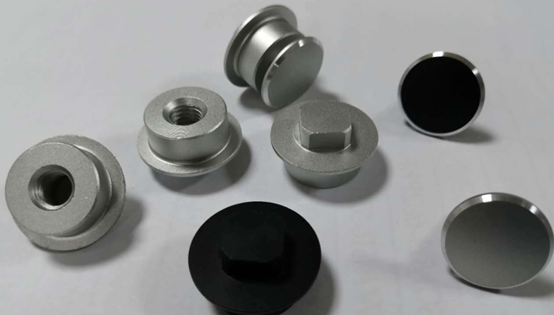